Hobbild celebrates 25 years!
Milling tools
Knowing which milling tool to use in machining is a very important aspect and we often find it difficult to understand what to use.
Many, after all the ups and downs for the choice or construction of the CNC milling cutter, find themselves in front of the first processes, and here the first problems and doubts arise:
Which tool do I use?
How fast am I going?
How many revolutions do I make the power tool go?

Normally you do the test with the first tool you have at hand, you try the machining that usually comes out bad and then you spend the night on the internet looking for useful news between forums and online tool catalogs, in the morning there we keep awake with confused ideas and with a thousand tests to do.
It's normal, we've been through it and we will all go through it this way.
The following are small tips and considerations based on my experience.
Let's start with the common terminology, often the tool that physically performs the machining is indicated with the name "milling", but the machine that performs the machining using the "milling tool" is also indicated with the same name "milling".
If you read somewhere: "I used a 2 millimeter cutter with two cutting edges", it means the use of a "cutter tool", if instead you find written: "I used a manual (or CNC) cutter with three axes for processing ”, means the use of a manual or CNC milling machine.
In the continuation of my exposition I will refer to the milling tool as “cutter”, but in any case it should be clear what I mean (I hope ..).
Before going into the specifics of the milling tools, I make a small passage on the machine on which the milling cutters are mounted, because it is important to understand what the mechanical limits of this may be, which then determine errors or problems in the processing phase, what I mean is soon said.
If the structure of the cutter is made of wood and with guides obtained from those of the drawers, we are probably in the presence of a not very rigid structure and with some play in the guides. hand, if you feel the game, it will be difficult to have very precise machining even on wood or plastic, and this regardless of the type of milling tool mounted.
Gaps during machining generate vibrations during cutting and consequently a machining not done well.
“No problem for this”, you tell me, “I have a metal cutter with a prismatic guide system and a high frequency power tool managed by an inverter”, a typical Chinese cutter.
Attention, this does not mean that there are no games or weaknesses.
I often see models of Chinese cnc cutters with prismatic guides, however, mounted on a sheet metal structure (low rigidity), or recirculating ball bushings cantilever mounted (mechanical horror), even power tool support brackets too thin (therefore flexes).
On the electrospindle then there would be a lot to write, I reverence the typical Chinese model with water cooling, often these models do not have bearings for axial loads, so they do not withstand much operations such as drilling.
Moral: touch, pull, move and check your machine to understand its consistency (obviously when turned off !!! _), knowing if it has or does not have games will then allow you to better evaluate the causes of incorrect processing.
And now the cutters.
There are thousands of types of cutters, understanding how to choose them according to the material to be machined requires a lot of experience, a myriad of factors can change even in a radical way, the final cut, I will not go into the detail of how a cutter works during the cut, however some basic information is required.

Main features

Let's see now the main characteristics of the cutter, and in particular the angles that are formed between it and the workpiece, specifically these angles are also called "spoils":
Cutting edge: it is the edge that cuts the material
Chest: It is the surface anterior to the cutting edge of the tool (a).
Front undress (γ): is the angle that forms in the front part of the cutting edge, where it detaches the shavings. The angle is defined by the vertical axis and the front chest of the tool. A tool is said to be POSITIVE when this angle creates a "ramp" for the chip. If on the contrary the chest tends to be inclined towards the front of the tool, and exceeds the vertical line, then we are talking about NEGATIVE tools, it is a very important angle that we will resume later, in the image the draft angle is POSITIVE.
Lower leaf (α): is the angle between the horizontal axis and the back of the tool (b). it is the rear part of the tool that leaves the removed area behind it, it must always be positive, otherwise it is said that "the tool is beading the material"
Cutting angle (β): is the portion of the tool between the bottom and the front rake. it is an important angle, sometimes if this angle is too small, it is said that "the tool is too greedy", that is, it gets stuck in the material.
Chip: (d) is the material removed.
Cutting direction of the tool: (c) in the case of our cutters it is a normally right-handed rotary motion.
Axial feed direction: (e) is the displacement that determines the depth of cut.
Positive (a) and negative (b) tool

Positive tools
Positive tools are used when we need a large cutting capacity and the absence of burrs on the edges. The more the tool is positive, the more these characteristics increase, to the detriment of tool life and its stability. It is used in non-ferrous and soft materials such as wood, plastic, brass and aluminum. The softer the material, the more we will need positive tools, one of the effects of positive tools is the reduction of the temperature in the cutting area. Using negative tools on plastic, for example, generates a lot of heat and the plastic tends to melt, thus negating the success of the processing.
Negative tools
Negative tools differ in their great resistance and some cases in their finishes (based on the material to be machined). They generate a lot of heat which can present a big problem. But their robustness makes them very useful for ferrous materials and steels in general. Another small drawback is due to the cutting effort which requires strength and cutting power.
In our cutters we would hardly go “deliberately” to use a negative rake tool.
To return to "ground to ground" on the choice of the tool and to go to simple, banal but understandable examples, let's try to see what type of knife we should use for three types of food:
Salami: very sharp knife, very small cutting angle (β), great skill of the operator in keeping a positive front rake angle.


Bread: knife very similar to that of salami, not necessarily sharp but certainly with a serrated edge.
Grana cheese: dull knife, very large cutting angle.

You understand that as for food, even with our cutters and for any type of material, we must use suitable cutter tools, if we try to cut the salami with the parmesan knife, it will be difficult to make a nice sandwich.
Main materials
Returning serious let's try to understand in what material the cutters can be made.
Broadly speaking, they can be made in HSS or Widia.
HSS (high speed steel) or super high speed steel , is a material widely used in the manufacture of metalworking tools (cutters and tools for the lathe, drill bits, discs for cutting metal pieces, etc.). The cutting properties of HSS tools are excellent, it should be noted that HSS steel is not a unique type of steel, but a category of steels, i.e. there are dozens of steels that can be generically called HSS.
Widia or also hard metal or Carboloy, is a material composed of hard particles of tungsten carbide embedded in a metal matrix (often cobalt).
It is produced through the sintering process, i.e. fine powders of the components are mixed, pressed and then heated while maintaining a high pressure so that the granules of the powders come together to form a single piece. This means that hard metals are not actual metals, but carbides (80-95%) bonded by a metal.
Hard metals are used to make tools for industrial processes with chip removal (turning, milling, drilling, tapping). Carbide tools are harder than super high speed steel tools (HV 1500 vs HV 1000) and withstand higher cutting temperatures (1000 ° C vs 600 ° C) allowing therefore higher processing speeds. A disadvantage of carbide is the lower toughness compared to high speed steel (they are more brittle).
Said thus, two conclusions could be drawn:
The first is that if my processes are mainly related to soft materials such as wood or plastic, I can use HSS cutters (cheaper), the second is that if I work more aluminum, brass or even carbon, I use Widia cutters.
In reality, however, materials such as aluminum or even brass, are better worked with HSS cutters, then wood, especially MDF or multilayer, is better if worked with Widia cutters because they last longer, wood seems an easy material, but wear the cutting edge of the cutter prematurely, in fact companies that work wood almost always even use diamond tools (inserts in industrial synthetic diamond).
How to recognize if a cutter is in HSS or Widia: I'll explain two simple methods, the first is based on the weight, a Widia cutter always weighs more than one in HSS, this is due to the greater specific weight of the material, the second method, probably the most practical, is that of use a simple magnet, the HSS cutters are very attracted to the magnet because they are basically made of steel, while those in Widia are very little attracted to the magnet, precisely because they are made of carbides and very little iron.


Coating of tools: You may have noticed that some cutters have a gold color, others are a dark gray.
These are surface coatings that make the tool surface much harder and greatly increase its wear resistance.
These coatings are of many types, they are based on titanium nitride, titanium carbo-nitride or even chromium nitride and so on, they are made on both HSS and Widia cutters.
Well, we have come to a good point but there are still the conclusions and the most important things that each of us wants to know.
Which cutters do I use for my work, where do I find them, how much they cost and how I use them, I bet you would have liked to read this part right away.
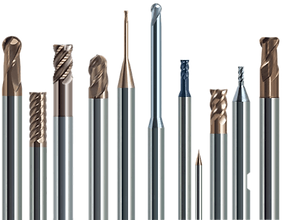
Choice of tool
"Which cutters do I use for my work?" when one asks me this question, I normally give this little pattern
"Diamond" type Widia cutters

Useful for: Balsa, carbon, depron, very soft wood, contouring of vetronite bases
Kress speed about 5, cutting speed about 400 mm / min, plunging speed about 300 mm / min
“Diamond” cutter so called because of its shape, recommended diameter 3.17 - 2.4 - 1.8 mm
Helical cutter with two hard metal cutting edges (Widia)

Useful for: hard wood, plastic plywood, also aluminum.
Kress speed about 5, cutting speed about 400 mm / min, plunging speed about 300 mm / min
Diameters from 3.17 to 6 or 8 mm
Helical cutter with one cutting edge in hard metal (Widia)

Aluminum, hard wood, plastic plywood.
Kress speed about 4, cutting speed about 400 mm / min, plunging speed about 300 mm / min.
For aluminum 1 mm thick, cutting speed about 120 mm / min, plunging speed about 80 mm / min, lightly lubricate the cut with "Svitol" spray or silicone oil
recommended diameter 3.17 - 3 mm
Burin cutter

Creation of PCB tracks, processing of text engraving on wood, plastic, aluminum
Kress speed about 4, cutting speed about 200 mm / min, plunging speed about 100 mm / min.
Cutter called "burin" with a hard metal edge (Widia), recommended diameter of 3.17, angle 60 ° and tip of 0.2 mm
Cutters kit

Then there are this kit of cutters available in many shopping centers, they are from Valex, they have a low cost, I use them to flatten, cut or profile, the tip bearing must be removed if used with CNC machines.
They are used on wood, MDF or plywood.
Useful information
Where do I find the cutters: I normally get them on Chinese online stores, they are cheap, low quality and consistency but they meet my needs, if I need something more efficient, I turn to specialized mechanical supply stores, here the costs multiply by 10, but the quality is much higher.
These shops are difficult to find, they sell directly to mechanical companies through representatives, they often do not sell to individuals or at least to those who are not VAT registered.
I am lucky because I work in the world of mechanics, but don't contact me for purchases !!!
The ideal is to have the friend or the friend of the friend representative of these companies, who in some way can advise you and provide the cutter suitable for your needs.
There are also Italian online shops that sell "professional" cutters for hobby use, but often resell Chinese products at higher prices.
On Ebay you can sometimes find good bargains, even on Subito.it you happen to see new tools at affordable prices.
How much do the cutters cost: by now you have read the answer between the lines above, if you take the cutters from China, the prices go to about 1.5 euros for Widia cutters with two cutting edges diameter 3.17 mm, for larger diameters yes it can reach 5-10 euros, considering the shipping costs included, I would say that they are excellent prices, but go and read my note on the Chinese Drills.
How to use the cutters: meaning at what speed of rotation, feed speed and depth of cut.
On this topic there are whole treatises on how to set the values, they are usually made by the manufacturers of such tools, specific for a certain type, with dimensions, material with which it is made, type of coating, material to be processed, required finish and much more . For example, if I have to make a blanking mold in tempered steel and I have to do some roughing operations, the catalog of the cutter manufacturer tells me which type of cutter to use and which cutting parameters I have to use with the machining.
We are talking about the use of professional numerical control machines in which special tools with a considerable cost are used and for typically mechanical precision machining.
In our case it is difficult to go to work steel with our pantographs, prohibitive to use professional cutters (they cost from 50 euros upwards), to then mount them on high-speed electrospindles where it is not possible to set and maintain a fixed rotation speed.
It is unlikely that a Chinese cutter seller will tell you that on the beech you should use a specific cutter at total revolutions, but that for the birch it is better to use another type of cutter, than on the plastic (but which type of plastic !!) it is better to go up. a two-flute cutter with 2 mm passes.
Also for woodworking there would be specific professional cutters suitable, but you understand that the costs are very high and in any case they are tools to be used on "real" pantographs.
If you go to the various forums looking for info, you will find very different opinions on what and how to use, maybe you will find those who give you the right advice because maybe they do this type of work by profession, how can you find the advice of those who "believe" to work well with a specific cutter model.
The moral is that only you can understand if a milling tool works well or not, if you have done something wrong or if you go too slow or fast with the cut, only with your experience, perseverance and reasoning will you be able to understand how to work.
Cutters from China: Great strength is that they are cheap and seem to be professionally made.
Sometimes one wonders where is the difference between these and the professional ones sold at a price 10-15 times higher.
The difference is there, and it often shows.
Let's start with the material with which they are made, mainly they are declared made in Widia, but there are hundreds of types of Widia depending on the quality and characteristics, needless to say that I do not think the quality of the material they are made of is the best, sometimes I see that they chip prematurely and wear out easily even just cutting wood.
Cut corners or bare, do you remember what is written above? They are VERY important angles and determine the good cut of the tool.
Depending on the material to be cut, these angles vary, but in Chinese cutters these angles are not indicated or in any case they are not respected when the cutters are made.
Some rake angles are not present, see photo on the side (the tool bead laterally).
I took the trouble to photograph some of my Chinese cutters with the microscope and I noticed that the front rake angle was negative, in fact when working with plastic material, the cut was very bad and he preferred to merge rather than cut himself.
The Chinese, when they make these mills, start with the correct sharpening wheels that make the right rake angles, but then they make thousands of mills without regrinding the wheels and therefore most of the mills do not cut well.
Regrinding the wheels, dimensional control and quality control have a cost .......
Sometimes we find Titanium coated Chinese cutters for longer life, but I have doubts about the quality of such coatings.
I use cutters from China, in 80% of my processes they are also good, but if I sometimes have problems, I understand that they may not be due to the type of cutter, but from its quality.

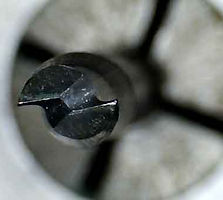