Hobbild celebrates 25 years!
ELECTRONICS FoamCutCNC
It must be combined with the DevCncFoam machine control program
It allows the control of a 5-axis machine (4-axis plus rotary table), and is complete with the entire wire heating control section.

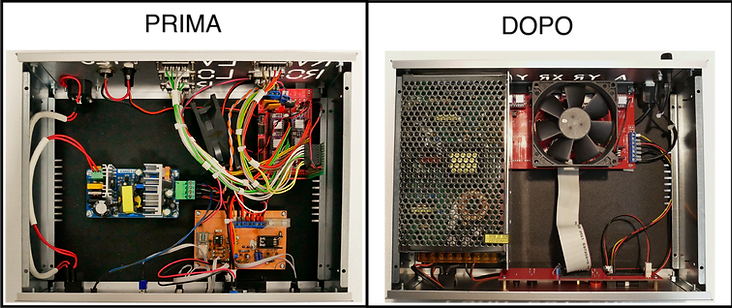
Cable management before and after adding the PCB
The advantages of this PCB are:
-
It can support up to 5 axes.
-
Ability to mount standard drivers used in 3D printers, see DRV8825, A4988, LV8729, TMC2130, TMC2225 and several others, all easily replaceable in case of failure.
-
You can mount Arduino Mega 2560 or Arduino Mega 2560 Embed (as in the photo), even these Arduino boards are easily replaceable thanks to the pin socket.
-
Optoisolated 12 V limit switches on the 4th axes, avoiding false signals due to the length of the cables.
-
Wire temperature control section by PWM system managed by a programmed PIC
-
Buzzer for acoustic signaling wire in heating (can be deactivated using a jumper)
-
Visual signaling led for heating wire
-
Possibility of having double power supplies for the motors and for the wire if its power voltage exceeds the maximum working voltage of the stepper drivers or a single unified power supply.
-
12V buck voltage reducer, inserted as a module, for the limit switch optocoupler section
-
Fuse for wire and motor power supply fuse
-
90mm cooling fan
-
Wire temperature control panel with display of wire supply voltage and current absorption
-
Variation of the wire temperature using two buttons, storage of maximum and minimum values and rest values, the set value remains in the memory even after switching off the board
-
Diverter for automatic or manual wire control operation
-
Manual heating of the wire even without a computer connection is useful for cleaning and checking the temperature of the wire
-
System indicator LED on
The most advantageous thing about this board is the almost total elimination of connection cables between connectors, board, Arduino, limit switches. This avoids as much as possible connection errors, false contacts and possible breakages of the driver modules and the Arduino board itself. Even the control panel, separated from the motherboard, allows easy positioning in a metal box